Das Werkstück für die funktionale Montage des vielversprechenden russischen PD-14-Triebwerks, das vollständig durch direktes Laserwachstum hergestellt wurde, wurde auf dem MAKS International Aviation and Space Salon vorgestellt. Dank des Einsatzes additiver Technologien konnte das Gesamtgewicht des Werkstücks um mehr als das Dreifache gesenkt und die Herstellungszeit auf 130 Stunden reduziert werden. Entwickler: St. Petersburg State Marine Technical University (SPbGMTU) und NUST "MISiS".
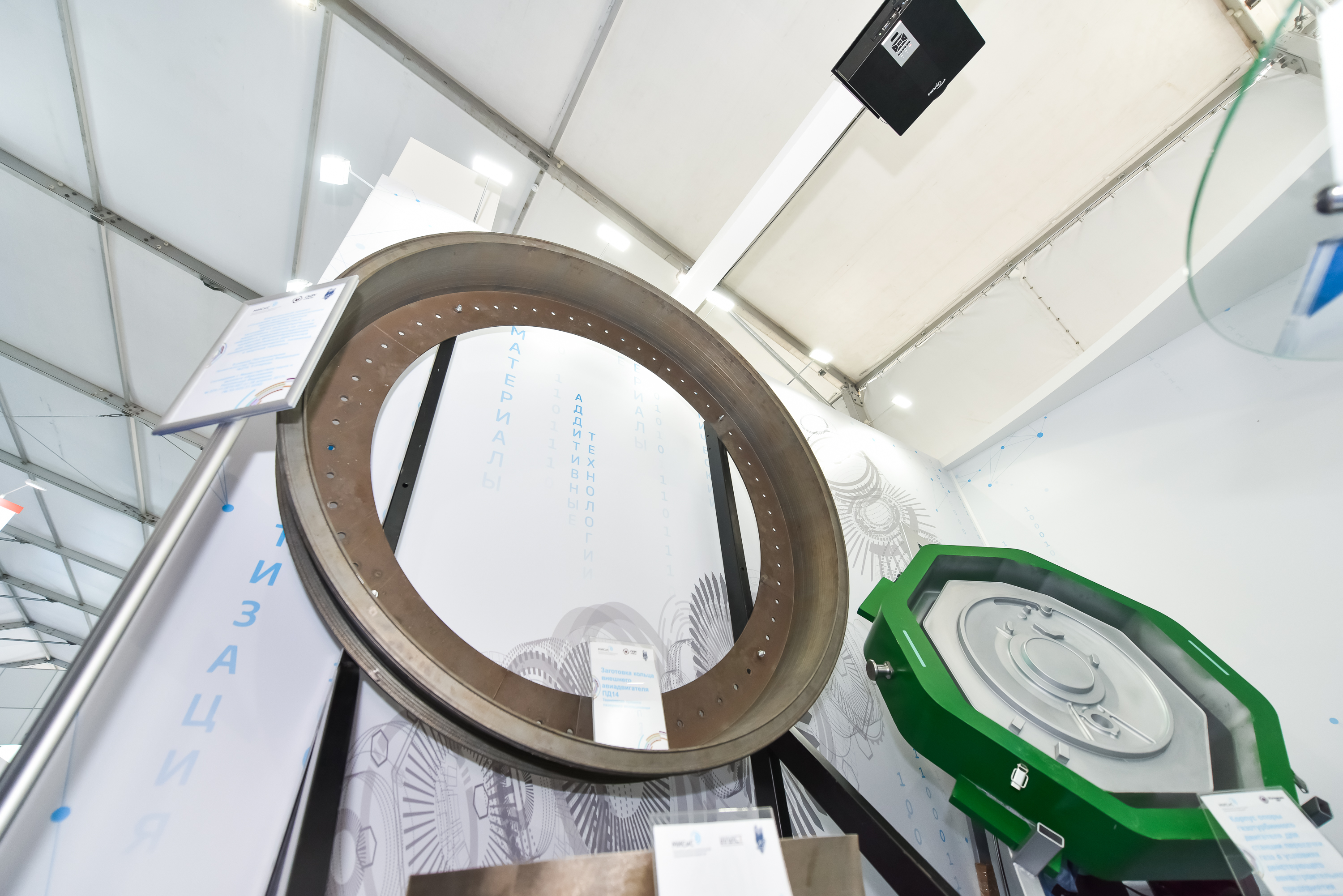
Die Schaffung wettbewerbsfähiger Flugzeugtriebwerke ist ohne die Verwendung von Materialien und Technologien der neuen Generation in ihrem Design nicht möglich. Wissenschaftler von SPbGMTU und NUST MISiS haben vorgeschlagen, die direkte Laserwachstumstechnologie zu verwenden, um den Außenring des PD-14-Motors zu erzeugen. Die erste experimentelle Probe des Werkstücks wurde bei SPbGMTU unter Verwendung einer einzigartigen Ausrüstung seines eigenen Designs hergestellt.
„Direktes Laserwachstum ist eine additive Technologie, die die Effizienz des Produktionsprozesses erheblich steigern kann. Zum Beispiel kann der Körper einer Brennkammer für ein kleines Gasturbinentriebwerk in 3 Stunden von Grund auf neu gewachsen werden, während die Herstellung mit herkömmlichen Technologien etwa zwei Wochen dauert. In unserem Fall dauerte die Erstellung eines Teilrohlings ungefähr 130 Stunden, obwohl die Abmessungen des Rohlings mehr als 2 Meter im Durchmesser betragen. Die Masse des Werkstücks hat sich mehr als verdreifacht. Dies bedeutet, dass das Volumen der nachfolgenden Bearbeitung drastisch reduziert wird, die Produktionszeit reduziert wird und die Produktionskosten reduziert werden, wodurch die Wettbewerbsfähigkeit der inländischen Flugzeugtriebwerke sichergestellt wird “, sagte
Andrei Travyanov ,
Direktor des EcoTech-Instituts von NISU MISiS.
Zur Herstellung des Außenrings des PD-14-Motors wurde eine Titanlegierung verwendet, die in Form eines Pulvers von einem Gasstrahl unter einem Laserstrahl zugeführt wurde, der ihn verschmolz und ein geschichtetes "Wachstum" des Teils ergab. Infolgedessen haben die Ingenieure die Phasen des Gießens, Schmiedens und Walzens des Werkstücks durchlaufen. Der Produktionsprozess beschleunigte sich um eine Größenordnung, während die mechanischen Eigenschaften des gewachsenen Materials Metallprodukten nicht unterlegen sind und die Eigenschaften von Gussprodukten erheblich übertreffen. Dies wird durch die Ergebnisse mechanischer Tests bestätigt, die sowohl in den Labors von NITU MISiS als auch in unabhängigen Labors, einschließlich des Central Factory Laboratory (TsZL, durchgeführt wurden )
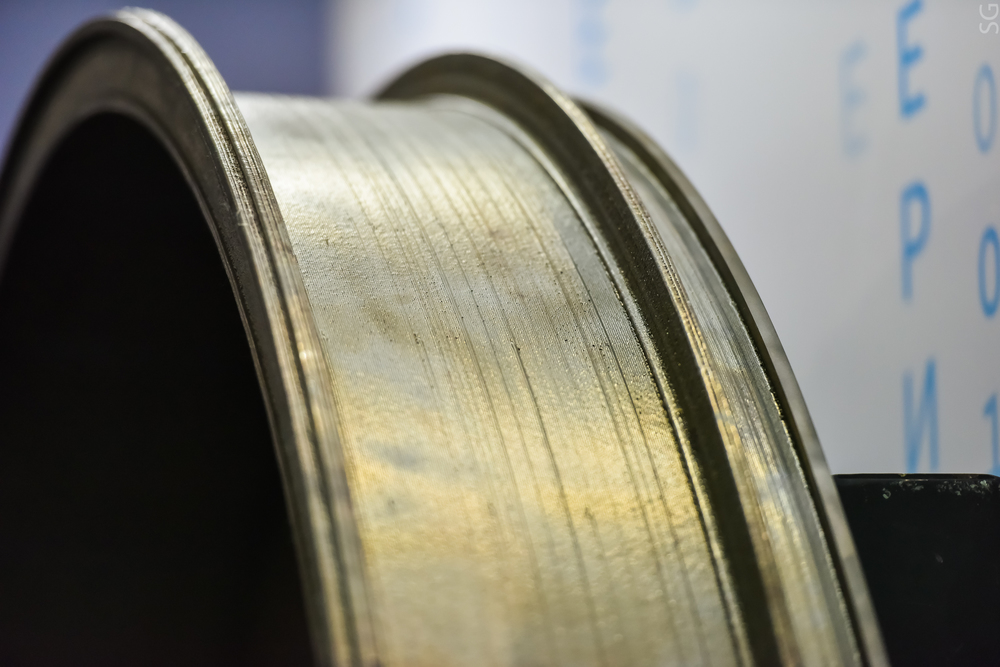
Ein weiterer technologischer Vorteil der Verwendung additiver Technologien bei der Erstellung von Luftfahrtteilen besteht darin, dass der Konstrukteur die Ergebnisse in Echtzeit sieht und die erforderlichen Änderungen schnell vornehmen kann. Der Prozess des Entwurfs und der Erstellung neuer Geräte mit dieser Methode wird um das Zehnfache beschleunigt. Die Technologie ermöglicht es, mehrere Gaspulverdüsen zu kombinieren und verschiedene Materialien in die Wachstumszone einzuspeisen, wodurch Produkte mit Gradienteneigenschaften erzeugt werden, dh ein Teil des Teils kann korrosionsbeständig und der andere hitzebeständig sein, was für die Luft- und Raumfahrtindustrie besonders wichtig ist.
„Der Herstellung dieser Probe gingen umfassende theoretische und experimentelle Studien voraus: Es wurden mathematische Modelle des Prozesses entwickelt, eine große Anzahl metallographischer Studien, Tomographie und Röntgenbeugung von Proben durchgeführt, mechanische Tests durchgeführt, optimale Modi und Wachstumsstrategien bestimmt, mehrere Modelle erstellt. Während des Wachstums des Prototyps wurden mehrere Modelle erstellt neue technische Lösungen, die derzeit unter Rechtsschutz stehen. Zum Beispiel das Wachsen mit einem horizontalen Laserstrahl unter Verwendung eines „dynamischen“ Substrats zur Bekämpfung von Rissen, technologische Methoden zur Steigerung der Prozessproduktivität, die Vorhersage thermischer Verformungen und deren Berücksichtigung im technologischen Modell des Produkts bei der Erstellung eines Steuerungsprogramms, um die erforderliche Genauigkeit der Konstruktion sicherzustellen “, betont der Projektleiter
Stellvertreter Evgeny Zemlyakov, Direktor für Forschungs- und Designtätigkeiten, Institut für Laser- und Schweißtechnologien, SPbGMTU .
Derzeit werden Tests für die resultierende Motorenbaugruppe auf der Grundlage eines der führenden spezialisierten Motorenbauunternehmen in Russland vorbereitet. Der Beginn der Industrieproduktion ist für 2020 geplant. Die gewonnenen positiven Erfahrungen werden es auch ermöglichen, die entwickelten Technologien bei der Konstruktion und Herstellung des PD-35-Motors einzusetzen.