La pièce pour l'assemblage fonctionnel du prometteur moteur russe PD-14, entièrement créé par croissance laser directe, a été présentée au Salon international de l'aviation et de l'espace MAKS. Grâce à l'utilisation de technologies additives, le poids total de la pièce a diminué de plus de trois fois et le temps de fabrication a été réduit à 130 heures. Développeurs: Université technique d'État maritime de Saint-Pétersbourg (SPbGMTU) et NUST "MISiS".
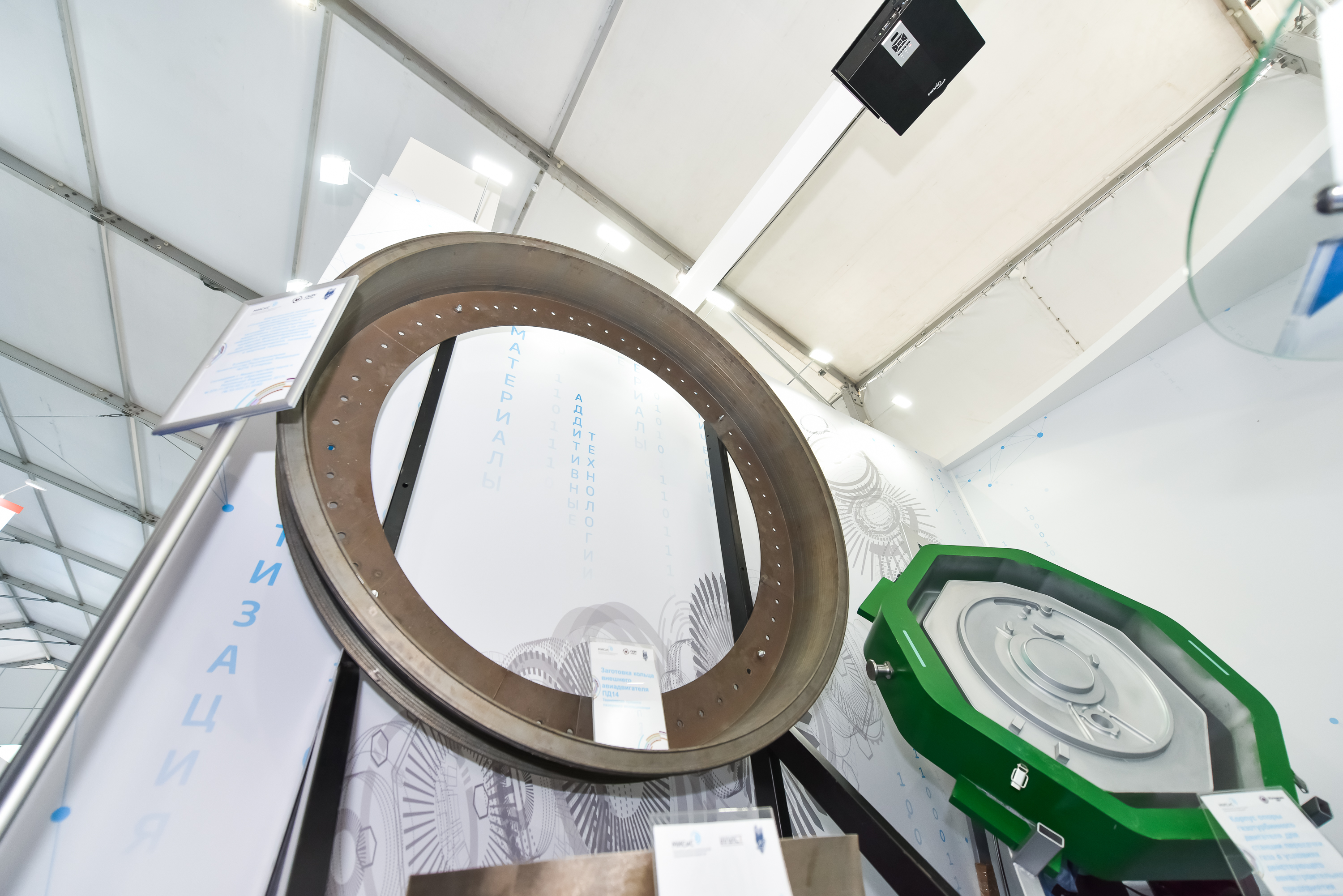
La création de moteurs d'avions compétitifs est impossible sans l'utilisation de matériaux et de technologies de nouvelle génération dans leur conception. Les scientifiques de SPbGMTU et NUST MISiS ont proposé d'utiliser la technologie de croissance laser directe pour créer l'anneau extérieur du moteur PD-14. Le premier échantillon expérimental de la pièce a été fabriqué à SPbGMTU en utilisant un équipement unique de sa propre conception.
«La croissance directe au laser est une technologie additive qui peut augmenter considérablement l'efficacité du processus de production. Par exemple, le corps d'une chambre de combustion pour un petit moteur à turbine à gaz peut être développé à partir de zéro en 3 heures, tout en utilisant des technologies traditionnelles, il faudra environ deux semaines pour le faire. Dans notre cas, il a fallu environ 130 heures pour créer une pièce brute, malgré le fait que les dimensions de la pièce brute dépassent 2 mètres de diamètre. La masse de la pièce a plus que triplé. Cela signifie que le volume d'usinage ultérieur est considérablement réduit, respectivement, le temps de production est réduit, les coûts de production sont réduits, garantissant ainsi la compétitivité des moteurs d'avion nationaux », a déclaré
Andrei Travyanov ,
directeur de l'Institut EcoTech de NISU MISiS.
Pour créer la bague extérieure du moteur PD-14, un alliage de titane a été utilisé, qui, sous la forme d'une poudre, a été fourni par un jet de gaz sous un faisceau laser le fusionnant, fournissant une "croissance" en couches de la pièce. En conséquence, les ingénieurs ont franchi les étapes de moulage, de forgeage et de laminage de la pièce. Le processus de production s'est accéléré d'un ordre de grandeur, tandis que les propriétés mécaniques du matériau cultivé ne sont pas inférieures aux produits métalliques et dépassent considérablement les propriétés des produits coulés, ce qui est confirmé par les résultats des tests mécaniques effectués à la fois dans les laboratoires du NITU MISiS et dans des laboratoires indépendants, dont le Central Factory Laboratory (TsZL )
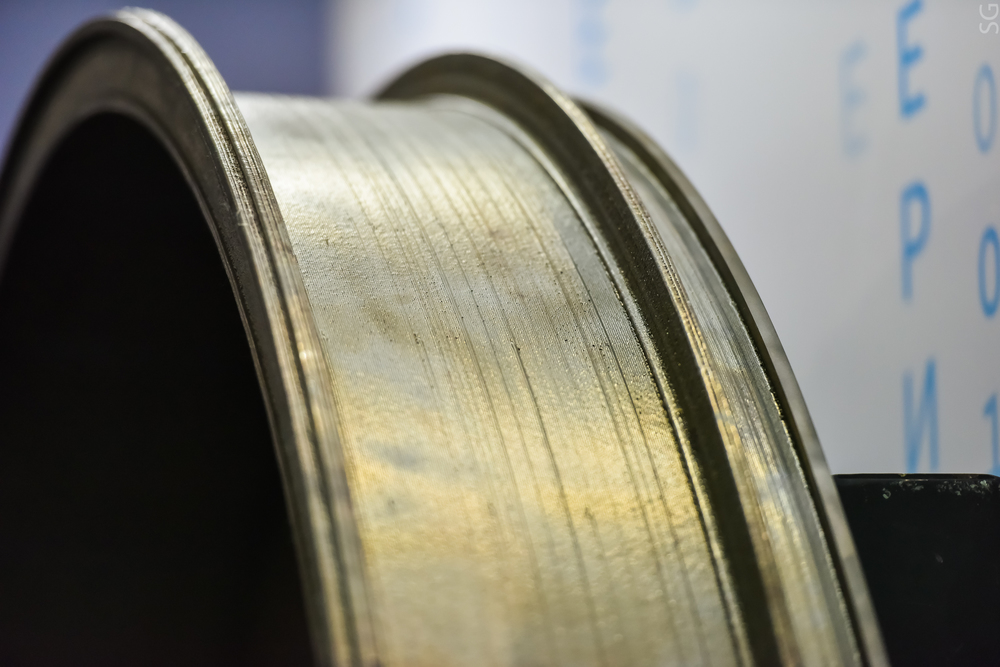
Un autre avantage technologique de l'utilisation de technologies additives dans la création de pièces aéronautiques est que le concepteur voit les résultats en temps réel et peut rapidement apporter les modifications nécessaires. Le processus de conception et de création de nouveaux équipements utilisant cette méthode est accéléré par des dizaines de fois. La technologie permet de combiner plusieurs jets de gaz-poudre et d'introduire divers matériaux dans la zone de croissance, créant ainsi des produits avec des propriétés de gradient, c'est-à-dire qu'une partie de la pièce peut être résistante à la corrosion et l'autre résistante à la chaleur, ce qui est particulièrement important pour l'industrie aérospatiale.
"La production de cet échantillon a été précédée par des études théoriques et expérimentales approfondies: des modèles mathématiques du processus ont été développés, un grand nombre d'études métallographiques, la tomographie et la diffraction des rayons X d'échantillons, des tests mécaniques ont été effectués, des modes optimaux et des stratégies de croissance ont été déterminés, plusieurs maquettes ont été réalisées. Au cours de la croissance du prototype, plusieurs maquettes ont été réalisées. de nouvelles solutions techniques actuellement sous protection juridique. Par exemple, croître avec un faisceau laser horizontal, utiliser un substrat «dynamique» pour lutter contre la fissuration, des méthodes technologiques pour augmenter la productivité des processus, prévoir les déformations thermiques et les prendre en compte dans le modèle technologique du produit lors de la génération d'un programme de contrôle pour assurer la précision de construction requise », souligne le chef de projet ,
adjoint Evgeny Zemlyakov, directeur des activités de recherche et de conception, Institut des technologies de laser et de soudage, SPbGMTU .
Actuellement, des tests sont en cours de préparation pour l'assemblage du moteur résultant sur la base de l'une des principales entreprises spécialisées dans la construction de moteurs en Russie. Le démarrage de la production industrielle est prévu pour 2020. L'expérience positive acquise permettra également d'utiliser les technologies développées dans la conception et la fabrication du moteur PD-35.